Introduction: Littleport’s Industrial buildings face unique challenges regarding roof maintenance and repair, particularly concerning roof leaks. These structures often have expansive roofs with complex designs and specific functionalities, making leak prevention and repair a critical aspect of facility management. Understanding the challenges involved can help industrial property owners and managers proactively address potential issues and maintain the integrity of their roofs.
Common Challenges in Industrial Roof Leak Repairs
- Large Roof Areas:
- Challenge: Industrial buildings typically feature extensive roof areas, sometimes covering several thousand square metres.
- Impact: Locating the exact source of a leak in such large roofs can be challenging and time-consuming, requiring thorough inspection and systematic troubleshooting.
- Complex Roof Designs:
- Challenge: Industrial roofs often have complex designs, including multiple levels, skylights, HVAC units, and other penetrations.
- Impact: Each design element presents a potential vulnerability for leaks, necessitating careful sealing and maintenance to prevent water ingress.
- Accessibility Issues:
- Challenge: Some parts of industrial roofs may require more work to access due to height, structural obstacles, or equipment installations.
- Impact: Limited accessibility can hinder inspection and repair efforts, potentially delaying response to identified leaks.
- Safety Considerations:
- Challenge: Industrial roofs require compliance with stringent health and safety regulations, particularly regarding work-at-height protocols.
- Impact: Ensuring the safety of maintenance personnel while conducting repairs adds complexity and may require specialised equipment and training.
Strategies for Effective Roof Leak Repair in Industrial Buildings
- Comprehensive Roof Inspections:
- Strategy: Conduct regular and thorough roof inspections by qualified professionals.
- Benefit: Early detection of potential leaks allows for proactive repairs before they escalate into more extensive damage, reducing downtime and operational disruptions.
- Utilisation of Advanced Technologies:
- Strategy: Incorporate advanced leak detection technologies like infrared thermography and moisture meters.
- Benefit: These technologies enable precise identification of moisture intrusion points, even in large or inaccessible roof areas, facilitating targeted repairs.
- Professional Roofing Expertise:
- Strategy: Partner with experienced industrial roofing contractors with a proven leak detection and repair track record.
- Benefit: Expert roofers possess the knowledge, skills, and resources to handle the complexities of industrial roof systems and ensure effective, long-lasting repairs.
- Proactive Maintenance Programs:
- Strategy: Implement proactive maintenance programs tailored to the specific needs of industrial roofs.
- Benefit: Regular cleaning, sealing, and maintenance of roof components, including drains, gutters, and flashings, help prevent leaks and extend the lifespan of the roofing system.
- Emergency Response Planning:
- Strategy: Develop and maintain an emergency response plan for rapid leak repair.
- Benefit: A structured plan ensures swift action in the event of a roof leak, minimising potential damage and operational downtime.
Conclusion: Addressing roof leak repair challenges in industrial buildings requires a proactive approach, combining regular inspections, advanced technologies, professional expertise, and proactive maintenance strategies. At Littleport Roofing Repairs, we understand the unique needs of industrial properties and offer comprehensive roofing solutions tailored to protect your investment and ensure the continuity of your operations.
.
Call us on: 01353 881 094
Click here to find out more about Littleport Roofing Repairs
Click here to complete our contact form and see how we can help you with your roofing needs.
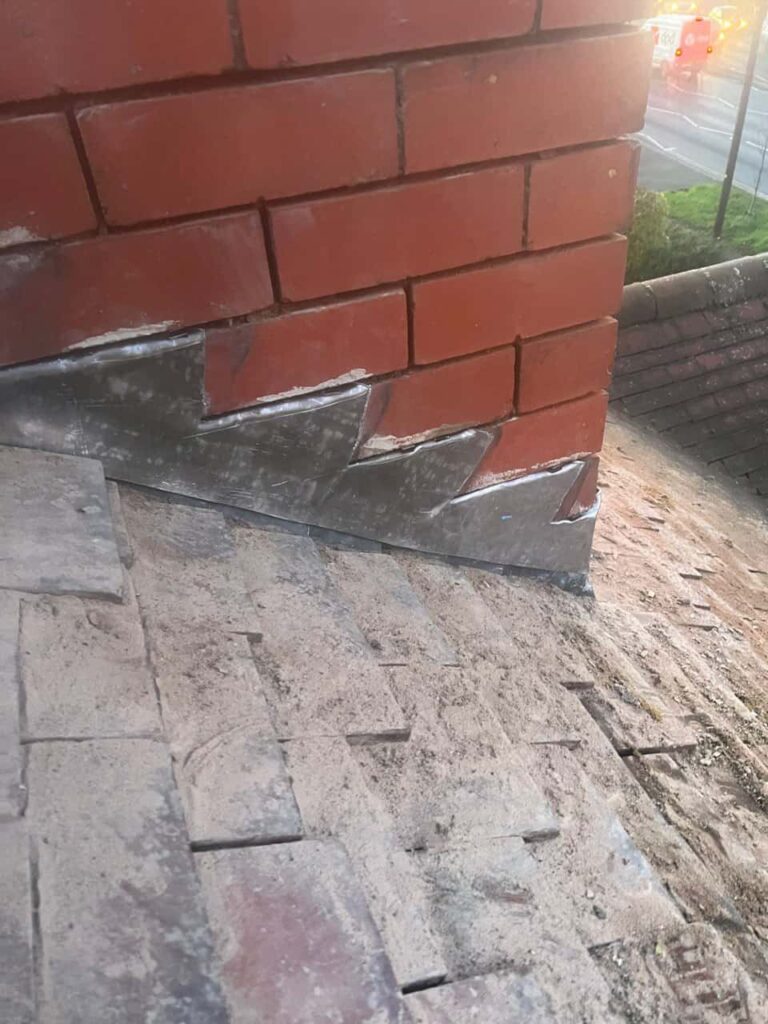